Bras de manutention robotisé pour positionner très précisément des composants de plusieurs tonnes à l’intérieur du Tokamak ITER
Chiffres clés
heures de travaux sur 3,5 ans
heures d'ingénierie
optimisation des coûts
Le contrat « Mechanical Handling Equipment for In-Vessel Assembly (MHE) » - enclenché en janvier 2016 – a pour but d’étudier, de réaliser et de qualifier les moyens qui seront utilisés pendant le chantier du réacteur de fusion ITER pour le montage des composants internes de l’enceinte à vide.
Les principaux constituants de MHE sont des systèmes de manutention de précision : In-Vessel Tower Crane (IVTC), Through-Port Transfer System (TPTS), outillages spécifiques, un banc de test à l’échelle 1 (Trial, Test & Training Facility - TTTF) simulant un secteur de l’enceinte à vide ITER, complétés par des plateformes d’accès opérateurs, des nacelles élévatrices de personnel.
A l’issue d’une procédure de consultation de deux ans, CNIM Systèmes Industriels a remporté le contrat MHE grâce à une grande inventivité pour proposer des solutions simples et des coûts de fabrication optimisés. Au mois de janvier 2018, ITER Organization a validé le design final de l’ensemble des équipements et CNIM Systèmes Industriels a commencé le montage du banc de test TTTF.
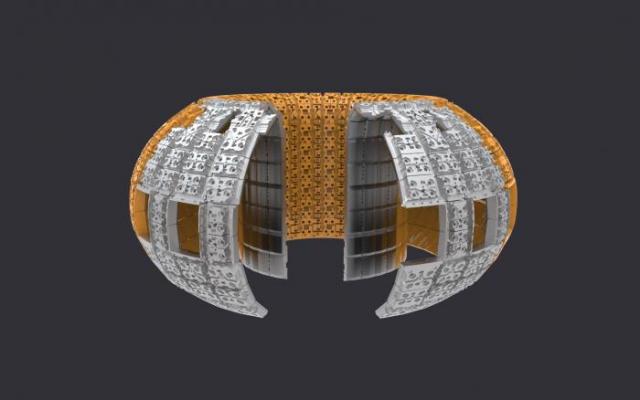
Garantir une mise en place fiable et sécurisée des composants
Au-delà de la conception et de la fabrication, ITER Organization a confié à CNIM Systèmes Industriels la responsabilité de la séquence d’assemblage des composants au sein de la chambre à vide, y compris la formation des opérateurs.
Le contrat MHE prévoit 3 lots de travaux, pour lesquels la fabrication de maquettes de composants et la validation des séquences de mise en place au sein du tokamak doivent être validées.
- Manutention et positionnement, au dixième de millimètre, des 440 boucliers antiradiations (« shield blocks ») - blocs d’1 m3 environ pesant 5 tonnes. Ils existent dans plusieurs configurations, l’une des plus contraignantes étant celle au plafond.
- Manutention et positionnement des réseaux de tubes « manifolds » - 7 m de long, 600 kg - nécessaires au refroidissement de l’enceinte à vide.
- Manutention et positionnement d’aimants « ELM coils » - 2 m x 4m, 1 tonne.
La grande diversité des composants (forme, poids, centre de gravité, position dans la chambre à vide) est un défi pour leur mise en place auquel répondent les systèmes de manutention développés par CNIM Systèmes Industriels.
(c)ITER Org
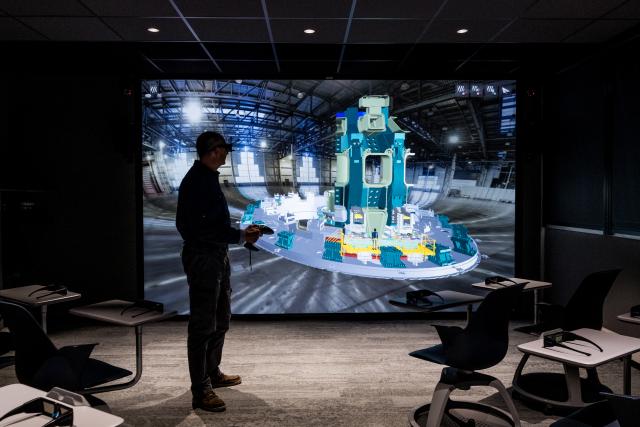
Une conception de très haut niveau : un environnement très encombré et confiné
Les ingénieurs de CNIM Systèmes Industriels ont réussi le défi de concevoir des systèmes capables de positionner des composants de plusieurs tonnes au sein du tokamak dans un environnement très encombré, en plus d’être soumis à des contraintes de propreté.
Le banc d’essai TTTF servira également de plateforme pour l’entraînement des opérateurs d’ITER pour les séquences de manutention et de montage.
Cinématique complexe
Si les systèmes et équipements du MHE doivent effectuer des opérations de cinématique complexe pour mettre en place les composants internes, il a fallu développer tout le savoir-faire de l’Ingénierie de CNIM Systèmes Industriels pour imaginer et concevoir leur procédé d’assemblage et de démontage. En effet à la fin du montage, les équipements MHE doivent être retirés du tokamak.
Le TPTS est capable d’acheminer tous les composants – pesant jusqu’à plusieurs tonnes - à l’intérieur du tokamak et de surcroît d’assembler et de démonter l’IVTC (système de manutention avec un bras robotisé de 8m de long et pesant 17 tonnes). Le démontage de l’IVTC a été un challenge d’ingénierie car une fois les composants installés, il y a d’énormes contraintes spatiales à l’intérieur de l’enceinte à vide.
Des matériaux spécifiques pour répondre aux exigences de l’ultra propreté
L’environnement ultra-propre de la chambre à vide a nécessité la conception des différents systèmes et équipements en matériaux spécifiques. Le zinc (principale protection des métaux contre la corrosion) ou encore les halogènes (très présents dans les polymères constituant les joints de roulement à bille, les boîtiers des capteurs ...) étaient interdits. L’acier inoxydable a été choisi pour les pièces en contact avec la chambre à vide et les composants du Tokamak. Des graisses et des polymères compatibles avec l’environnement spécifique du Tokamak ont par ailleurs dû être trouvés.
Des systèmes et équipements aux performances singulières
Les deux principaux systèmes de manutention de précision sont le « Through-Port Transfer System (TPTS) » et le « In-Vessel Tower Crane (IVTC) ».
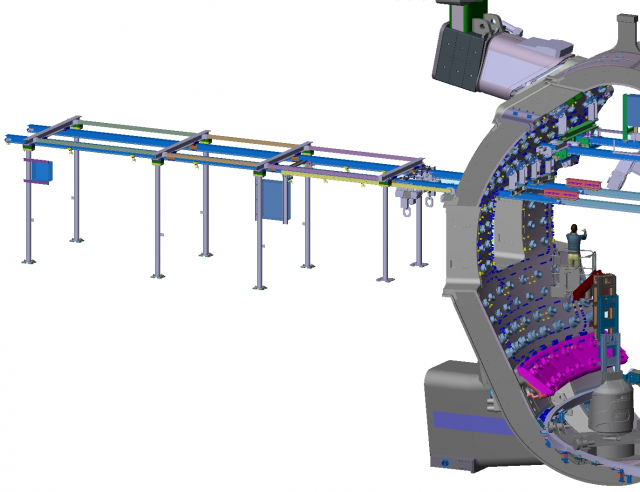
Système de transfert de composants
Le TPTS est un système de transfert des composants internes vers l’intérieur / l’extérieur du tokamak via des portes très étroites (4m² environ) avant leur prise en charge par d’autres moyens de manutention tel que l’IVTC. Les composants internes de la chambre à vide, doivent être transférés et basculés avec la plus grande précision et stabilité. Le TPTS a une capacité de levage de 5 tonnes et de 2 à 8 m de haut. De conception FEM*, il garantit un fonctionnement sécurisé et une stabilité pendant le transfert. ITER Organization a particulièrement apprécié la robustesse et la simplicité de la conception de cet outillage.
*FEM : Fédération Européenne de Manutention : normes de fabrication sur équipements de manutention
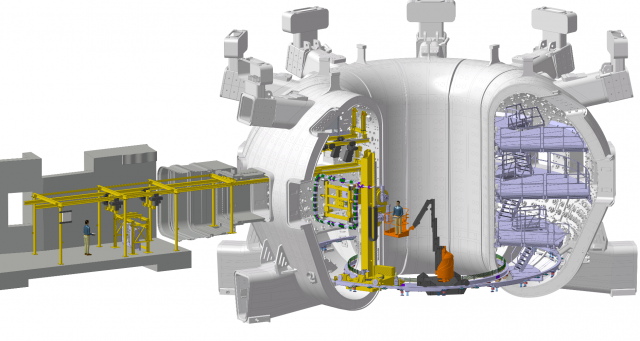
Système de manutention mobile haute précision
Après avoir été porté à l’intérieur du tokamak par le TPTS, les composants sont réceptionnés par l’ITVC. Ce système de manutention mobile précis permet leur montage sur la paroi de l’enceinte à vide. Également conçu selon les normes FEM, l’IVTC est un bras de manutention multiaxes (8 mouvements sont possibles dont 5 motorisés) de 7m de haut, se déplaçant sur des rails circulaires, et piloté à distance. Pesant près de 17 tonnes à vide, ce système positionne au dixième de millimètre près des composants de plusieurs tonnes.
Tester à l'échelle 1 les phases d'assemblage et de démontage
Enfin le « Trial, Test & Training Facility (TTTF)” est une installation d’essai, de test et de formation des outillages. Il simule un secteur d’enceinte à vide à l’échelle 1. Il mesure 11 m de haut, 37 m de long et 16 m de large.
Après la qualification des procédés d’assemblage et de démontage dans les ateliers de CNIM Systèmes Industriels, l’ensemble TTTF sera monté à Cadarache sur le site d’ITER afin de former les opérateurs avant leur intervention en conditions réelles.
Ainsi, fin 2019, le banc de test TTTF a été monté entièrement sur le site CNIM Systèmes Industriels. Les essais du TPTS se sont déroulés avec succès durant l’été 2020, puis suivront ceux de l’IVTC début 2021.
L’ensemble des essais de mise en place des composants, notamment ceux des blocs antiradiations et des aimants ELM, sera finalisé mi 2021.