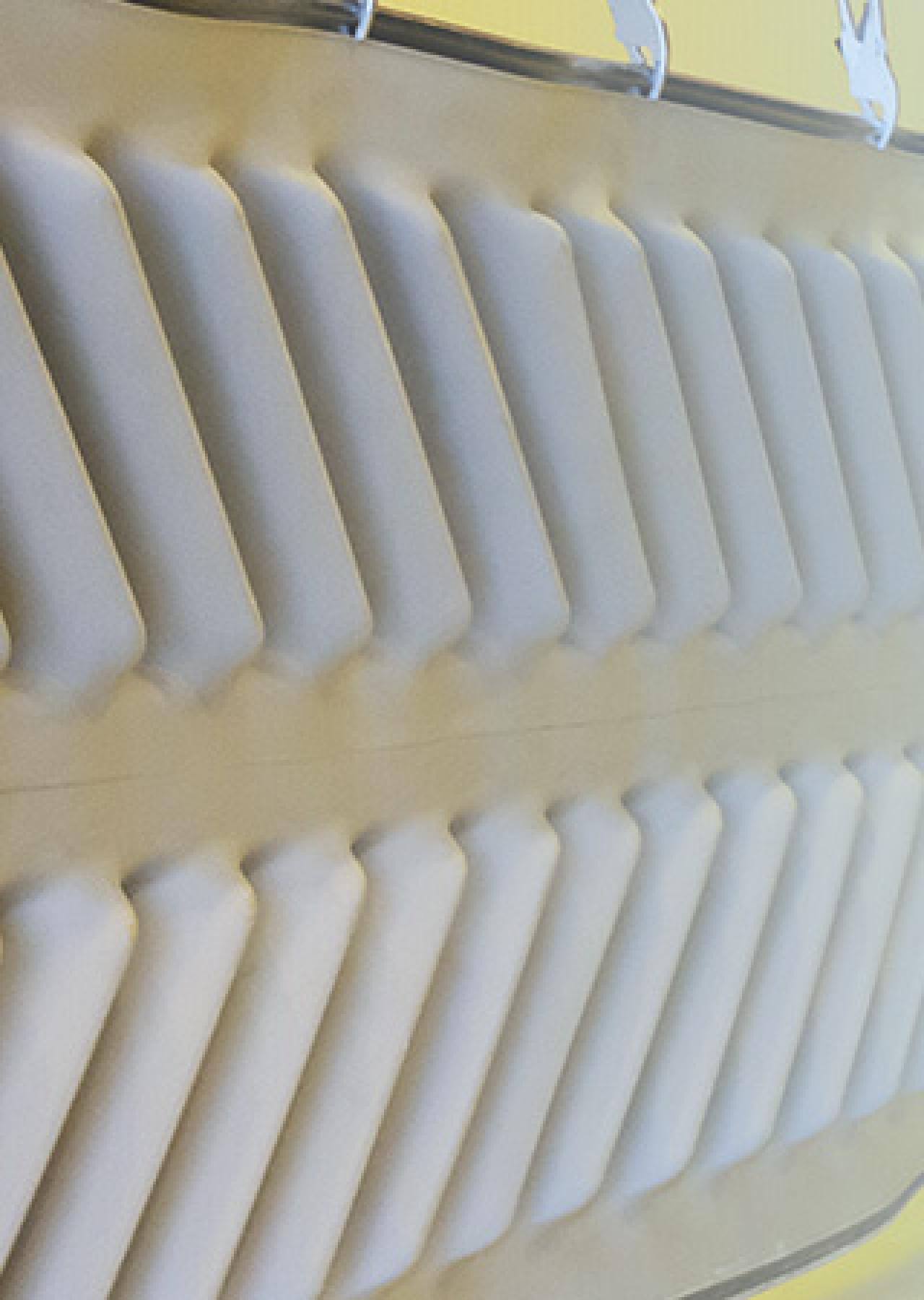
La membrane d’étanchéité de l’arche de confinement de la centrale nucléaire de Tchernobyl
Chiffres clés du projet
mois de fabrication pour 2 km de membrane
Vitesses des tornades de niveau 3 auxquelles résiste la membrane
de capacité d’allongement
Le consortium NOVARKA, formé de Bouygues Travaux Publics et de Vinci Construction Grands Projets, a construit une arche de confinement pour la centrale nucléaire de Tchernobyl sinistrée lors de la catastrophe de 1986.
Sur la base d’un concept élaboré par NOVARKA, CNIM Systèmes Industriels a effectué la qualification et la fabrication d’une membrane en polyuréthane longue de 2 km, assurant la fonction de double joint d’étanchéité entre la nouvelle enceinte et l’ancien sarcophage.
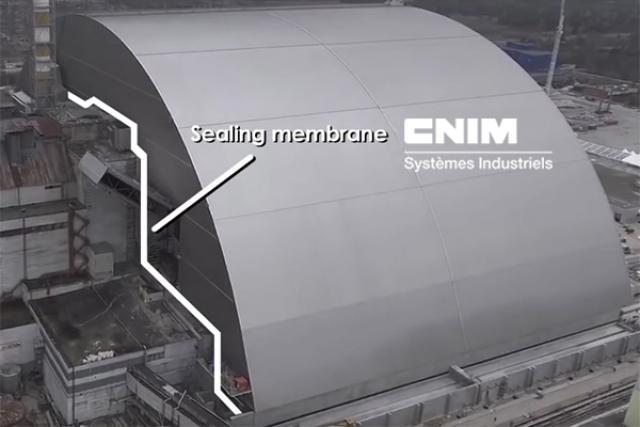
Un élément clé pour assurer le confinement
La membrane assure une scellée hermétique du sarcophage empêchant que les particules radioactives ne soient libérées dans l’atmosphère.
Vérifiée par de nombreux tests, la membrane résiste à l’épreuve des dégradations provoquées par les radiations ou des évènements climatiques extrêmes.
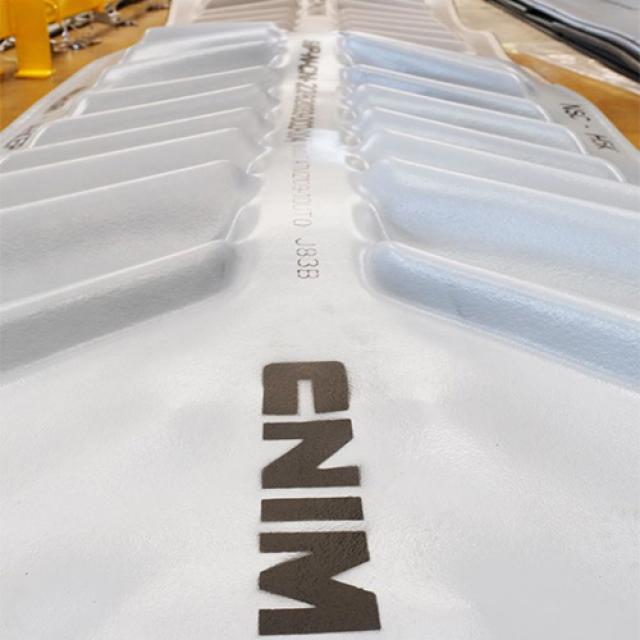
Un concept unique pour répondre à des exigences de sécurité majeures
Fruit d’une longue expérience de CNIM Systèmes Industriels dans la fabrication de grande dimension et la maîtrise des matériaux haute performance tel que le polyuréthane, la membrane possède toutes les caractéristiques d’un équipement hors-norme.
Elle atteint une longueur cumulée de 2 km, sur 1,5 m de large pour s’adapter à l’hyper structure de l’arche.
Ses très grandes souplesse et résistance lui permettent de résister à des tornades avec des vents allant jusqu’à 330 km/h.
Elle conserve ses propriétés mécaniques en dépit des contraintes générées par l’environnement hostile pour une durée de vie de 30 ans.
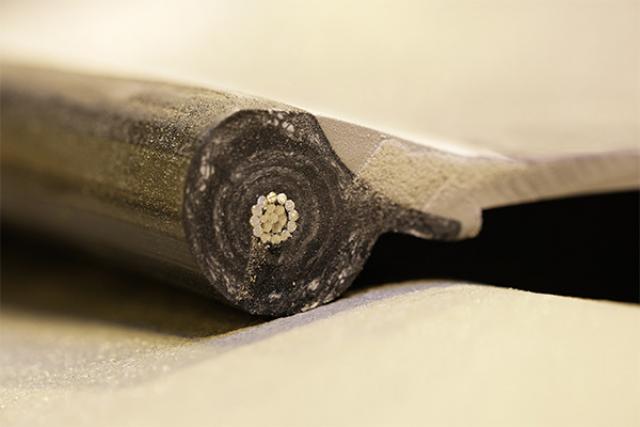
Un design et un matériau innovants pour une résistance à toute épreuve
Les caractéristiques propres au polyuréthane en font le matériau idéal pour la sécurité :
L’élastomère conserve ses propriétés mécaniques sous l’effet des UV, d’écarts de température importants ou d’efforts très intenses.
Pour stopper la propagation des déchirures, CNIM Systèmes Industriels a innové et breveté un design en double chevron ainsi qu’un système de pinces (flanges*) qui permet de lier hermétiquement les deux pans de membrane.
*Flange: un système innovant pour lier hermétiquement deux structures
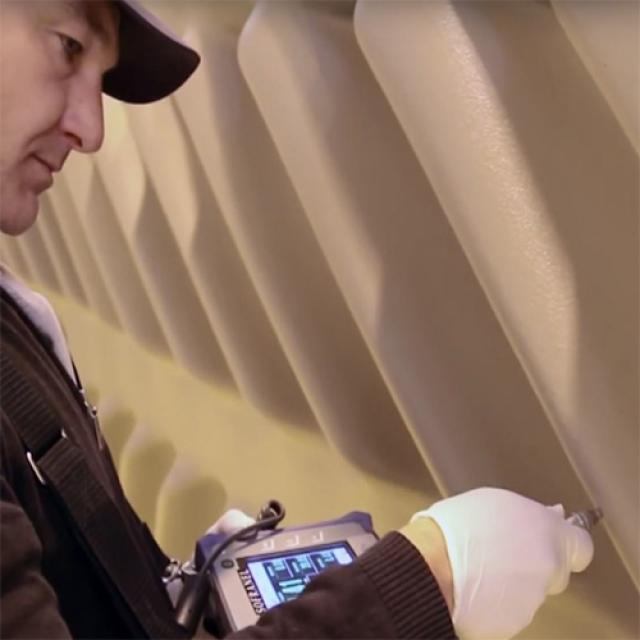
La qualification par CNIM Systèmes Industriels : un gage de sûreté
Des tests réalisés à échelle 1 ou en laboratoire de chimie des matériaux confirment des prévisions annoncées lors des calculs préparatoires et de la modélisation :
- Test d’élongation en cas de dilatation ou de contraction de la matière sous l’effet de la chaleur.
- Test sur des éprouvettes vieillies à une exposition aux radiations équivalente à 30 ans.
- Test de résistance à la fatigue sur une machine d’étirement réalisant 2 millions de cycles à 5HZ.
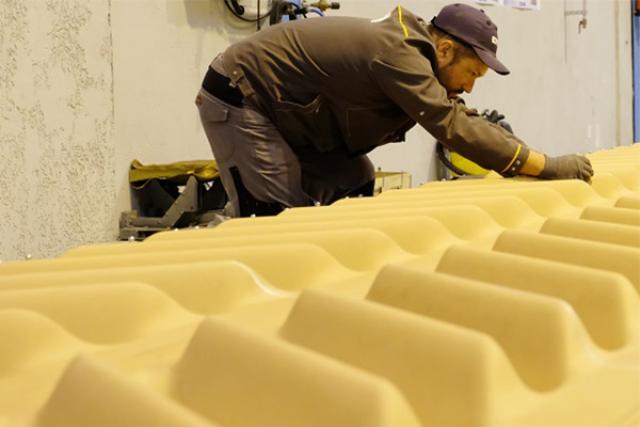
Une conception sur-mesure
Afin d’épouser parfaitement la géométrie de l’arche, chaque segment de la membrane, long de 16,5 m, est unique. CNIM Systèmes Industriels a fabriqué des moules spécifiques à chacun pour suivre au plus près les critères de qualité : épaisseur, qualité de la matière, aspect…
Pour les besoins du projet, CNIM Systèmes Industriels a également investi dans une chaîne robotisée de projection de polyuréthane sur son site industriel de la Seyne-sur-Mer.
Polyurethane spraying
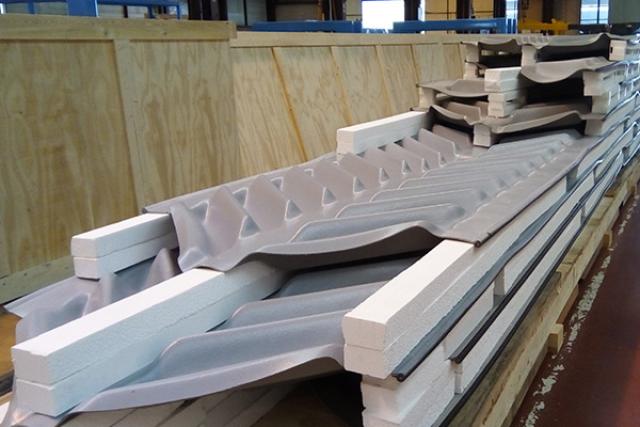
Un accompagnement global
CNIM Systèmes Industriels a été présent sur l’ensemble des étapes de conception, qualification, production et installation sur site.
L’exposition au rayonnement limitant la présence d’opérateurs, un banc de test et d’entrainement a donc été réalisé afin de permettre aux opérateurs de répéter les séquences d’installation.