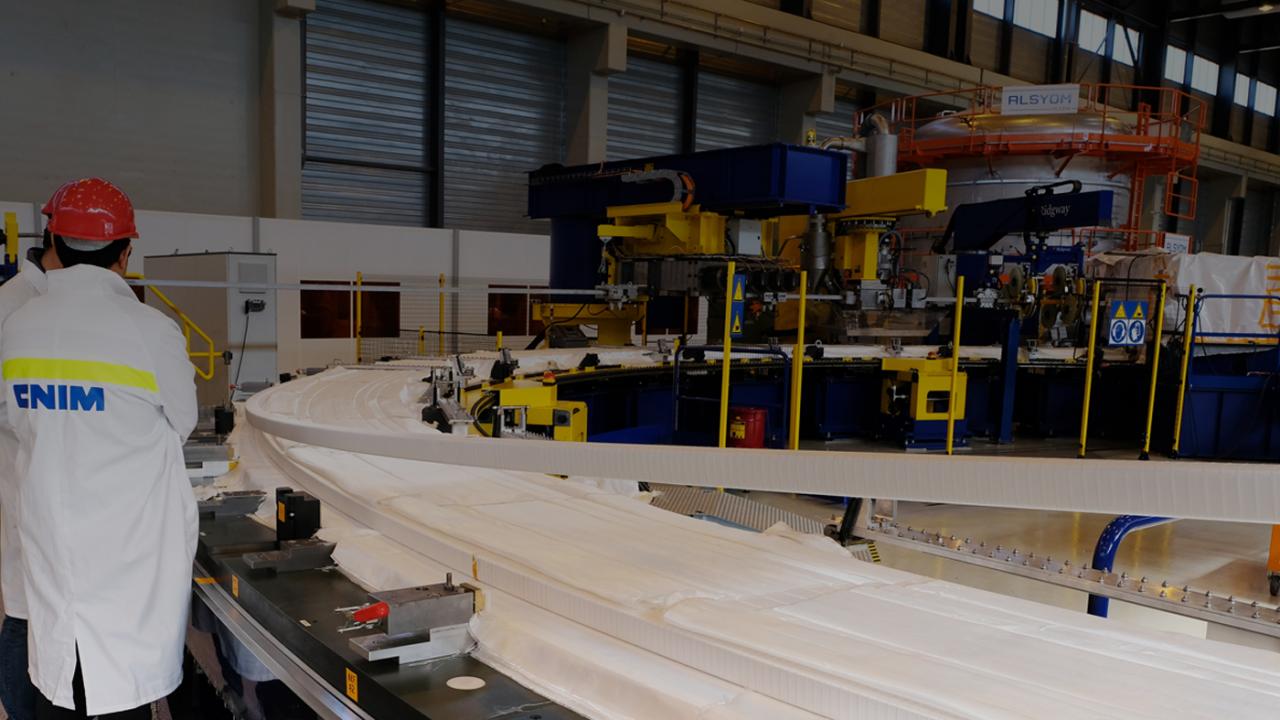
Manufacturing of superconducting magnets weighing more than 350 tons
Key figures
Diameter of the biggest superconducting magnets
Cumulative length of superconducting cable wounded by CNIM Systèmes Industriels
CNIM Systèmes Industriels' employees involved on the project
The international ITER program, based in Cadarache (Bouches du Rhône, France) is a major international scientific project demonstrating the power of fusion as a large, unlimited and safe energy source. CNIM Systèmes Industriels is actively contributing to this project through several design, manufacturing and installation contracts..
In 2015, F4E entrusted CNIM Systèmes Industriels with the Poloidal Field Coil Manufacturing contract for the manufacturing of 4 of the 6 Poloidal Field Coils (PF Coils) superconducting magnets designed to create the "magnetic cage" which will help maintain the shape and stability of the plasma in the reactor. They measure between 18 and 25 meters in diameter and weigh up to 384 tons.
7 manufacturing stations for the PF Coils : a dedicated workshop on ITER's site © F4E, ITER ORG
Maintaining the shape & the stability of the plasma
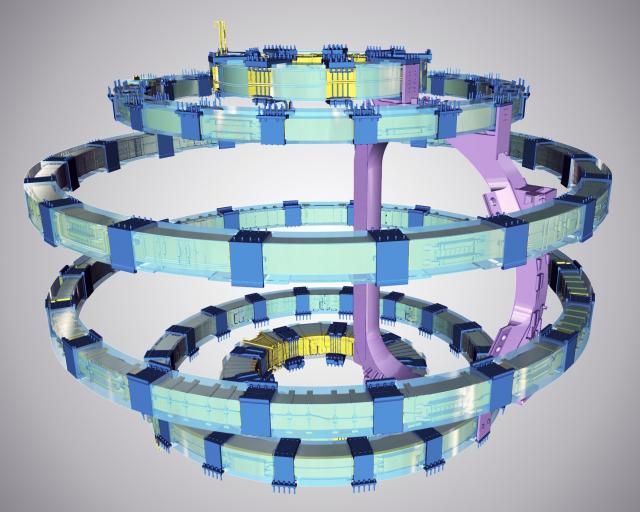
PF Coils are poloidal field magnets designed to keep the ultra-hot plasma (150 million degrees Celsius) away from the walls of the reactor and contribute to its shape and stability.
Six PF Coils in total will be positioned outside the toroidal magnetic structure: 2 are manufactured by Chinese and Russian companies, the 4 central magnets, the biggest, are manufactured by CNIM Systèmes Industriels and ASG.
Picture : 6 PF Coils (in blue) positioned horizontally around the ITER vacuum vessel. The 4 biggest are manufactured by CNIM Systèmes Industriels and ASG © ITER Org
A complex manufacturing process
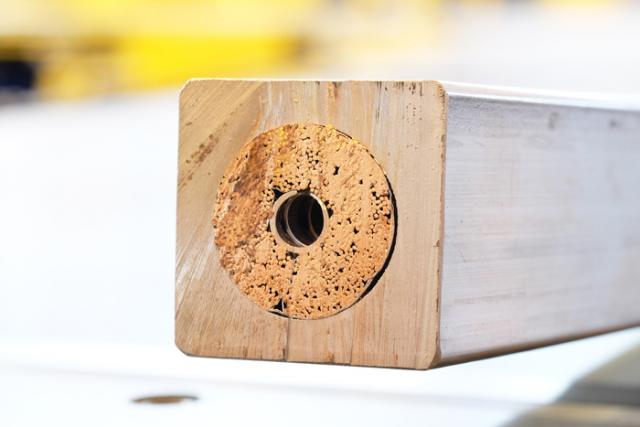
The largest coils are manufactured by CNIM Systèmes Industriels in collaboration with ASG, an Italian company specialized in the production of magnets, on the ITER site in a dedicated 250 m long building, the PF Building. The PF Building is composed of 8 manufacturing stations, each station is dedicated to a specific task.
Each magnet consists of "double pancakes" made of niobium-titanium superconducting cables.
Section of the superconducting niobium-titanium cable © CNIM Systèmes Industriels
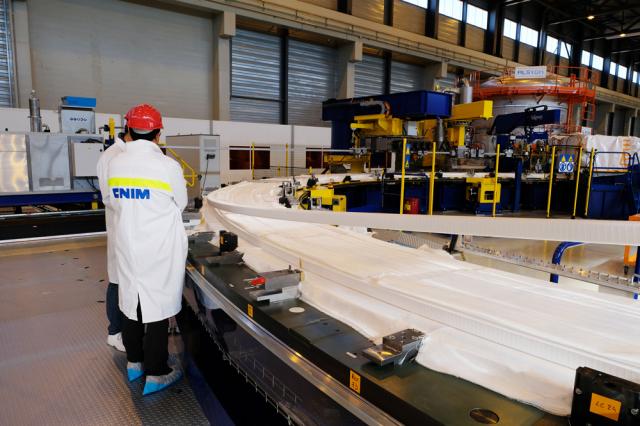
Delivered in 20-tons spools, the conductor is uncoiled and straightened before passing through cleaning and sandblasting machines that prepare its surface to receive several layers of glass-fibre insulating tape. Rotating tape heads enter into action as the conductor, fed from two spools simultaneously, joins the tooling table to be "turned" into the precise dimensions required for each coil. A double pancake is thus formed.
Winding operation of the superconducting cable © CNIM Systèmes Industriels
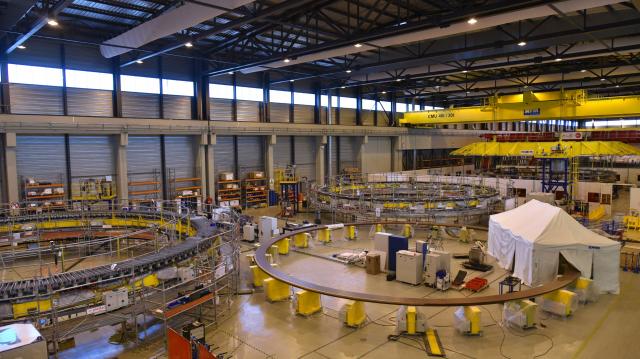
The double pancake is transported by overhead crane to the vacuum pressure impregnation station and lowered into a custom-fit mold. Epoxy resin, injected over the course of several hours, fills all gaps and hardens the glass tape under the effect of heat and pressure. The resulting structure is rigid and homogeneous, providing excellent electrical insulation and mechanical strength.
The manufacturing process of a PF Coil - from winding activities to final assembly - will take approximately two years per coil.
Picture : Impregnation station, one of the 8 building stations © CNIM Systèmes Industriels
Constant adaptability
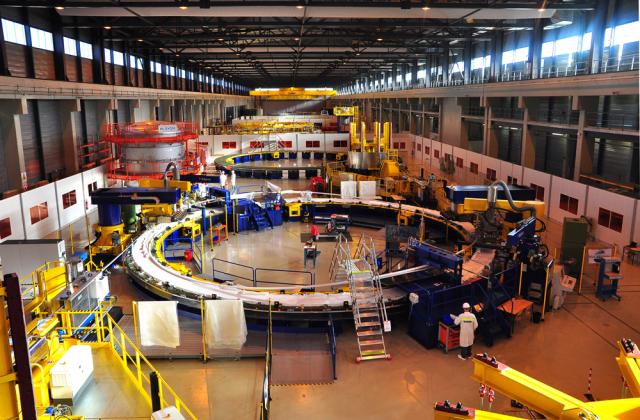
CNIM Systèmes Industriels has demonstrated its ability to set up a manufacturing workshop on its client's site in Cadarache and to work in a multi-contract and multilingual environment.
CNIM Systèmes Industriels works upstream the product's life to manufacture very high precision "double pancakes" on the first 4 stations. CNIM Systèmes Industriels’ team must make constant adjustments given the highly innovative nature of the project. CNM Systèmes Industriels is also in charge of the production and supply of parts for the manufacture and assembly of PF Coils: purchasing and/or welding and/or pre-assembly.
Indeed, CNIM Systèmes Industriels has been working on the ITER site for many years now and is involved in numerous contracts, including the contract for the manufacture of radial plates. Innovation and adaptability are part of our DNA.
Tests were carried out at different scales to validate the processes and verify the proper functioning of machines.
Picture : PF Coils building stations on ITER's site © ITER Org, F4E
A dedicated team set up on site
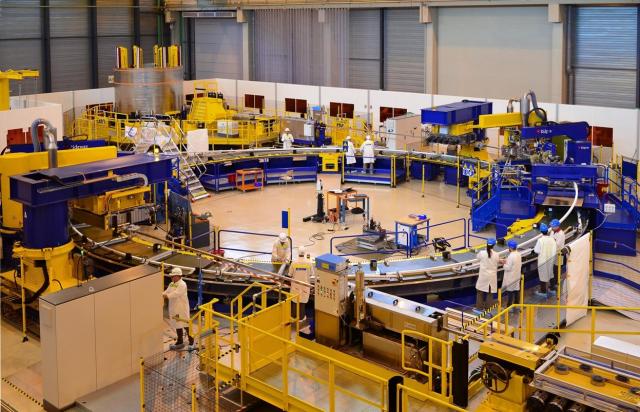
More than 50 CNIM Systèmes Industriels employees are working in Cadarache to ensure the success of the ambitious PF Coil project.
CNIM Systèmes Industriels has set up a complete team of experts dedicated to the success of the project: station operators, supervisors, welders, quality controllers, workshop manager, planner, scheduling, methods, project manager, etc. The key skills of our teams are mobilized for the success of this ambitious project.
Project management is at the heart of CNIM Systèmes Industriels' DNA, our teams are able to design, industrialize and manufacture projects from A to Z with high added value.
Photo : Winding of a supraconducting magnets © CNIM Systèmes Industriels
For CSI the project is done
On December 7, 2022, the CSI teams completed the manufacturing of the 30th Double pancake, marking the end of 7 years of collaboration with F4E. This part was delivered to ASG which will complete its transformation into PF Coil on the last 4 manufacturing stations.
From 2023, the PF Coils will be installed in the tokamak using the lifting beam system designed and manufactured by CNIM Systèmes Industriels as part of the contract Purpose Built Tool. The lifting beam system is a specific tooling for handling components up to 700 tons and 17m high.
Picture : Representatives of F4E, ITER Organization welcoming the sixth Poloidal Field coil on-site, ITER site, Cadarache, June 2020 © F4E