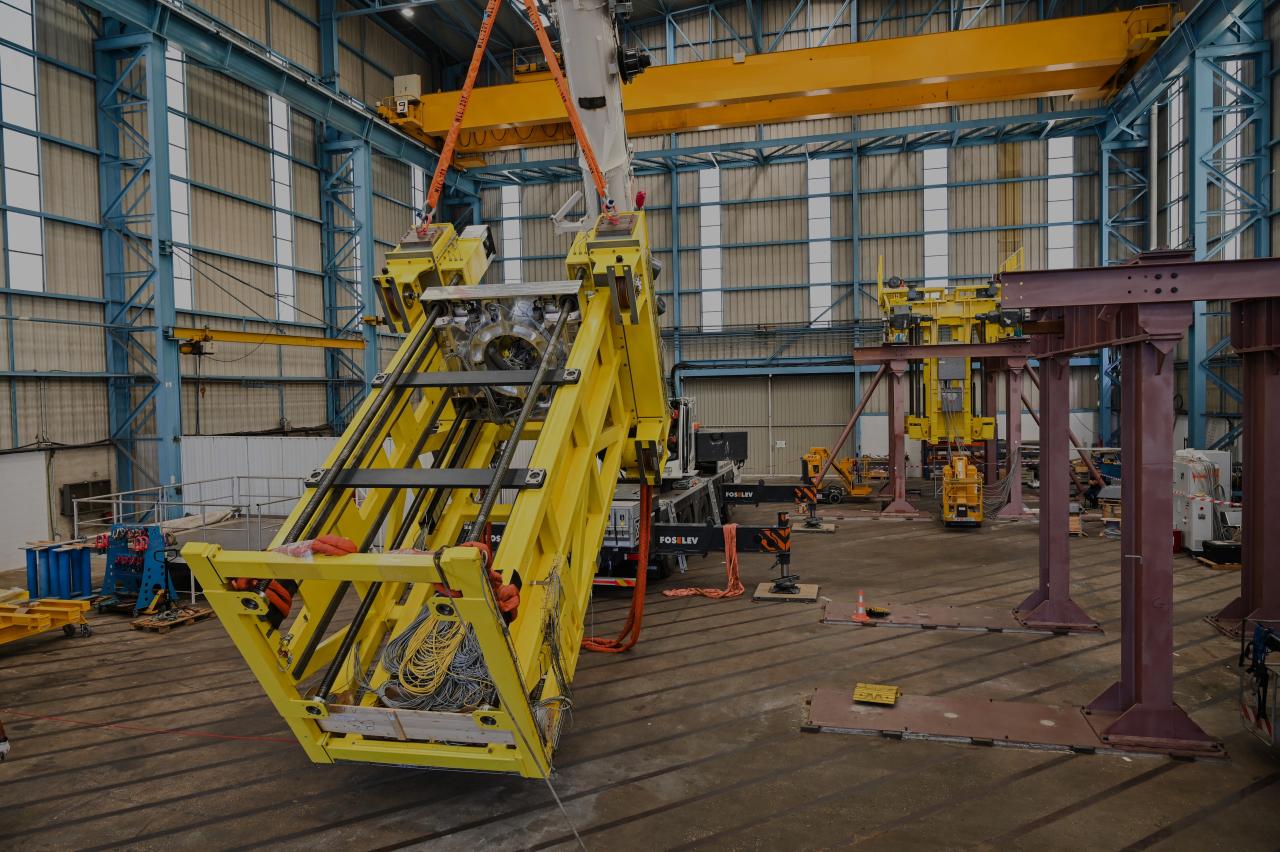
Fuel handling systems for deep storage
CNIM Systèmes Industriels designed and manufactured 3 nuclear fuel handling machines for the Olkiluoto site in Finland.
Key figures
special machines
weight : up to 30 tons
positioning precision
3 safe fuel handling machines
Onkalo is the geological storage facility for Finnish nuclear fuel at the Olkiluoto site. In 2017, Posiva Oy, a joint venture of Finnish nuclear utilities TVO and Fortum, entrusted CNIM Systèmes Industries with the development of three fuel handling and transfer machines: the "Cask transfer Trolley", the "Fuel Handling Machine" and the "Canister Trolley".
The role of machines
Intended for the ONKALO® Encapsulation Unit at the Onkalo deep landfill site, the 3 handling and transfer machines have the following roles:
- the "Cask Transfer Trolley" is designed to transport the casks carrying the fuel assemblies under the hot cell;
- the Fuel Handling Machine is dedicated to transferring fuel assemblies from the transportation cask to their copper casks, via a drying station;
- the "Canister Trolley" conveys the copper casks under the various stations (welding, machining, inspection), before taking them to the buffer zone, prior to the elevators for descent into the galleries, 500 meters below the granite.
The machines are made of S355/ 304L steel. They are 6-7m high, 4-6m wide, 3-6m long, and weigh between 20 and 35 tonnes. They can be operated remotely.
A design adapted to Finnish and international requirements
"The CSI teams were able to adapt to the quality and nuclear safety requirements of STUK - the Finnish nuclear safety and radiation protection authority," says Romain Septfons, CSI project manager. "Our experience in the safe handling of fuel, notably through the SFCTF - our spent fuel handling cart, enabled us to offer our customer the best possible solution".
Precise positioning
The casks and drums handled are around 5 m long and have to be positioned to the nearest millimetre," explains Gregory Ecalle, one of CNIM Systèmes Industriels' design experts. For the "Canister Trolley", for example, its extremely precise positioning performance is achieved thanks to a system of tri-directional cylinders, placed on a lower rotating plate. Our expertise in electromechanical systems for safe handling in constrained environments enables us to find solutions that are both innovative and robust.
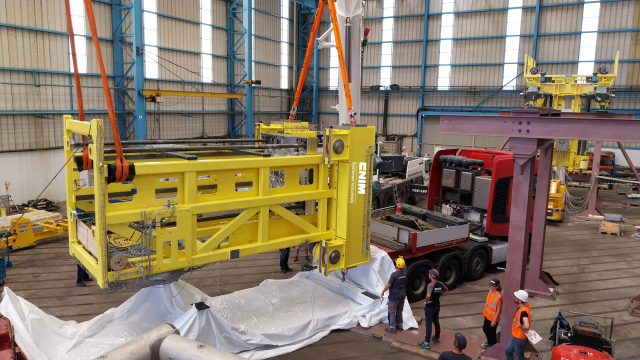
Delivery of the 3 machines : all CSI professions involved
At the end of August 2023, the 1st machine, the Canister Trolley, was delivered, weighing 34 tonnes, 3.5 m wide, 7 m high and 4 m long. It will be commissioned by our colleagues in the REEL Group. The REEL International teams will operate directly from a specially set-up office on site.
The other two machines were delivered during the 1st semester of 2024 are currently being installed.
In the end, the Canister Troller was loaded onto a truck from one of CSI's workshops, with an accuracy of just a few cm. 1 bridge and 1 crane were needed, as well as the precise positioning of the truck driver and the guiding ropes managed by the CSI teams. 3 hours of handling for a successful loading.
We would like to thank our client for its confidence!
CSI's vertical integration is an asset for this type of project
All of CSI's trades were involved in the creation of this extraordinary handling system," emphasizes Romain Septfons. It's a project that has mobilized the entire design office, as well as the Methods & Industrialization department. Then my colleagues in Purchasing, Order Control and Manufacturing (machining, boilermaking) were heavily involved. Finally, it was the turn of the electrical wiring and performance testing teams to get to work. CSI's vertical integration is an asset for this type of project.