Robotic handling arm for the precise positioning of multi-ton components inside the ITER Tokamak
Key figures
hours of work over 3,5 years
hours of engineering
optimisation of costs
The purpose of the Mechanical Handling Equipment for In-Vessel Assembly (MHE) contract — triggered in January 2016 — is to study, produce and qualify the resources to be used during work on the ITER job site for the assembly of the internal components in the vacuum chamber.
The main MHE components consist of precision handling systems : In-Vessel Tower Crane, Through-Port Transfer System and special tools, a scale 1 test bench (Trial, Test & Training Facility — TTTF) simulating a sector of the ITER vacuum vessel, and operator access platforms, aerial work platforms.
Following a two-year consultation procedure, CNIM Systèmes Industriels won the MHE contract because of its inventiveness in offering simple solutions and optimized manufacturing costs. In January 2018, ITER Organization approved the final design for all the equipment and CNIM Systèmes Industriels began assembling the TTTF test bench.
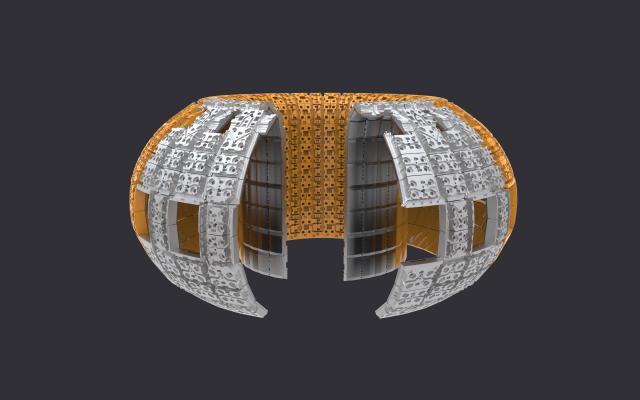
Ensuring safe and reliable installation of components
As well as the design and manufacture, ITER Organization has entrusted CNIM Systèmes Industriels with responsibility for the component assembly sequence in the vacuum chamber, including operator training.
The MHE contract provides for the following three work packages, for which the fabrication of component mock-ups and the validation of the installation sequences within the tokamak must both be validated.
- Handling and positioning — to within a tenth of a millimetre — the 440 radiation shield blocks, each of which is a cubic metre in size and weighs approximately five tonnes. These exist in several configurations, one of the most demanding being the ceiling units.
- Handling and positioning the manifold networks needed to cool the vacuum vessel. Each manifold is seven metres long and weighs 600 kg.
- Handling and positioning the ELM coil magnets, each of which is 2 m x 4 m in size and weighs a tonne.
The wide range of components (shape, weight, centre of gravity and position in the vacuum chamber) makes for a challenging installation by the handling systems developed by CNIM Systèmes Industriels.
(c)ITER Org
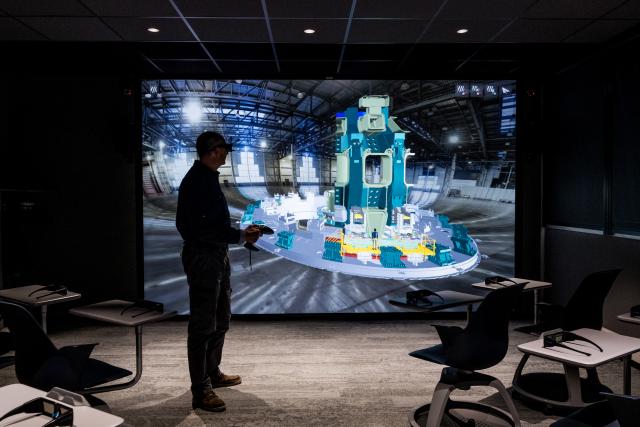
Very high-level design : highly crowded and confined environment
CNIM Systèmes Industriels engineers have succeeded in designing systems for positioning components weighing several tonnes within the highly crowded confines of the tokamak while also meeting extremely stringent cleanliness constraints.
The TTTF test bench will also serve as a platform for training ITER operators on the handling and assembly sequences.
Complex kinematics
As MHE systems and equipment must perform complex kinematic operations to install the internal components, it was necessary to develop all CSI’s engineering know-how in order to imagine and design their assembly and disassembly processes. At the end of assembly process, the MHE equipment must be removed from the tokamak.
The Through-Port Transfer System is capable of transporting all the components — some weighing several tonnes — inside the tokamak as well as assembling and disassembling the IVTC, a handling system with an 8-metre-long robotic arm weighing 17 tonnes. Dismantling the IVTC presented a serious engineering challenge because once the components are installed, there are enormous spatial constraints inside the vacuum vessel.
Special materials for extreme cleanliness constraints
The vacuum chamber’s ultra-clean environment demanded the design of entirely new systems and equipment in special materials. Zinc (the normal means of protecting metals against corrosion) or halogens (a major constituent of the polymers used in making ball bearing seals, sensor boxes, etc.) were prohibited. Stainless steel was chosen for all parts in contact with the vacuum chamber and the tokamak components. Greases and polymers compatible with the tokamak’s very special environment also had to be found.
Exceptionally efficient systems and equipment
The main two precision handling systems are the Through-Port Transfer System (TPTS) and the In-Vessel Tower Crane (IVTC).
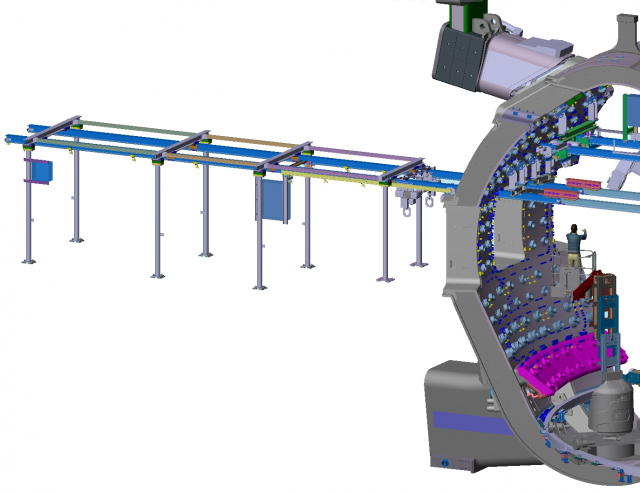
System for transferring internal components
The TPTS is a system for transferring internal components into and out of the tokamak through very narrow doors (approximately 4 m²) before they can be handled by other handling equipment such as the IVTC. The vacuum chamber’s internal components must be transferred and tilted with extreme precision and stability. Consisting of seven hoists, the TPTS has a lifting capacity of 5 tonnes between 2 and 8 m high. Designed by the FEM*, it guarantees safe, stable operation during transfers. ITER Organization particularly appreciated the robustness and simplicity of its design.
*FEM : European material handling federation
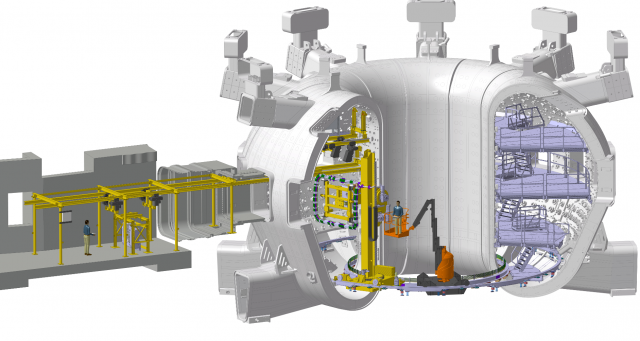
Precision handling of heavy loads
Once the TPTS has transferred the components into the tokamak, they are received by the ITVC. This precise mobile handling system then assembles them on the wall of the vacuum vessel. Also designed to FEM standards, the IVTC is a remotely controlled, multi-axis handling arm 7 metres high and offering eight movements, five of which are motorized, moving along a circular track. Weighing almost 17 tonnes unladen, this system positions components weighing several tonnes with an accuracy of a tenth of a millimetre
Life-size testing of the assembly and disassembly phases
Lastly, the Trial, Test & Training Facility (TTTF) is a trial, testing and training facility for the equipment. Simulating a life-size vacuum vessel sector, it measures 11 m high, 37 m long and 16 m wide.
Once the assembly and disassembly processes have been qualified in the CNIM Systèmes Industriels workshops, the TTTF assembly will be installed in Cadarache on the ITER site to train operators before they begin working under real conditions.
As soon as the customer validated the design in January 2018, CSI began the procurement and manufacturing of the various MHE systems.
Consequently, by the end of 2019 the entire TTTF test bench was installed on CSI's site. The TPTS trials were successfully completed in the summer of 2020 and these will be followed by those of the IVTC in early 2021.
All component installation tests, particularly those of the shield blocks and ELM coil magnets, will be finalized in mid-2021.