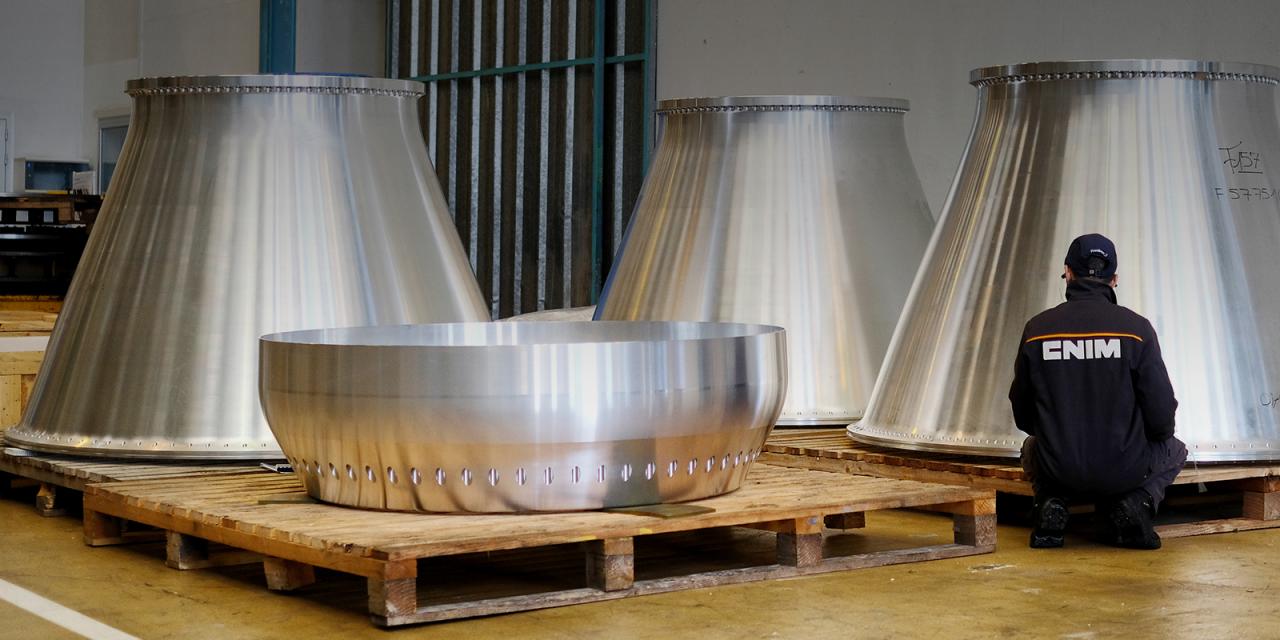
Nozzle casings for Ariane 5 launcher
Key figures
nozzle casings manufactured for Ariane 5
18-year partnership between ArianeGroup & CNIM
manufacturing tolerance
Between 2004 and 2022, CNIM Systèmes Induistriels has contributed to the reliability* of the Ariane 5 rocket by manufacturing all of the metal structures for the Ariane 5 nozzles. CNIM Systèmes Industriels has produced more than 200 nozzle casings for the space player.
* "Ariane 5, the most reliable launcher on the market, holding the record for the number of successful consecutive launches” (Source ArianeGroup)
Ariane rockets and CNIM Systèmes Industriels nozzle structure CNIM ©ArianeGroup
The Ariane 5 boosters are made up of a main body and its nozzle. Located at the base of the thrusters, the 2 nozzles evacuate and guide the propulsion gases during the rocket's first flight phase.
Nozzle structures are made up of 3 parts, called "casings", assembled together. Subsequently, other parts are added inside the casings to form the complete nozzle.
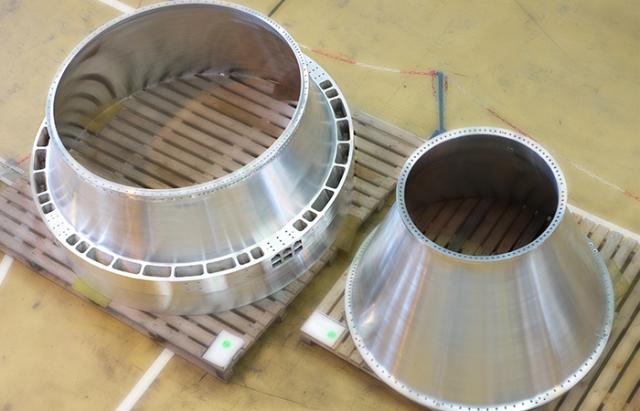
High precision, large size and flawless parts.
Production challenges lied in the manufacturing delay, large-scale machining precision and in the final sealing of the nozzle.
In 9 months, CNIM Systèmes Industriels carries out all the manufacturing stages of the Ariane 5 nozzle casing, from the raw material order to delivery to the customer. On average, 7 Ariane 5 rockets were produced per year to put satellites into orbit; i.e. 14 sets of casings per year to be manufactured by CNIM Systèmes Industriels.
The machining of casings for space applications required a very high precision with a manufacturing tolerance of 0.01 mm on parts up to 3 m in diameter, 1.5 m high and weighing 800 kg *
*characteristics of the downstream casing.

Very high precision 3D controls
CNIM Systèmes Industriels has large-scale metrology machines to meet ArianeGroup's quality requirements. The operating modes of the manufacturing processes have been specially designed to meet the very high precision required on the parts.
All the casings were checked in 3D in an air-conditioned metrology room.
Dye penetrant inspection
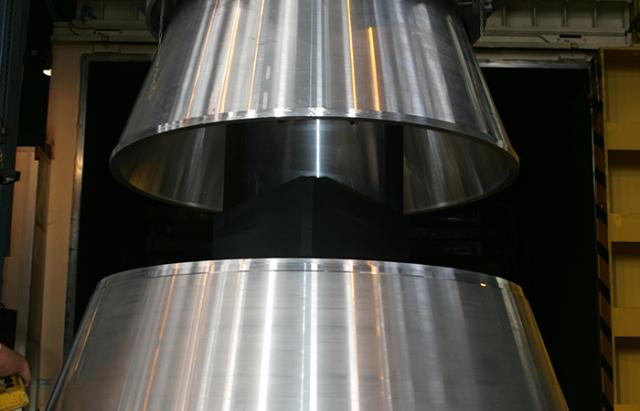
Electron beam welding and large dimension machining
Until 2008, CNIM Systèmes Industriels used electron beam welding to assemble the downstream casing (see photo below). Then CNIM Systèmes Industrielssupplied untreated moulded parts and machined them before checking them and delivering them to ArianeGroup.
Electron beam weld assembleing the downstream casing.
Large turning