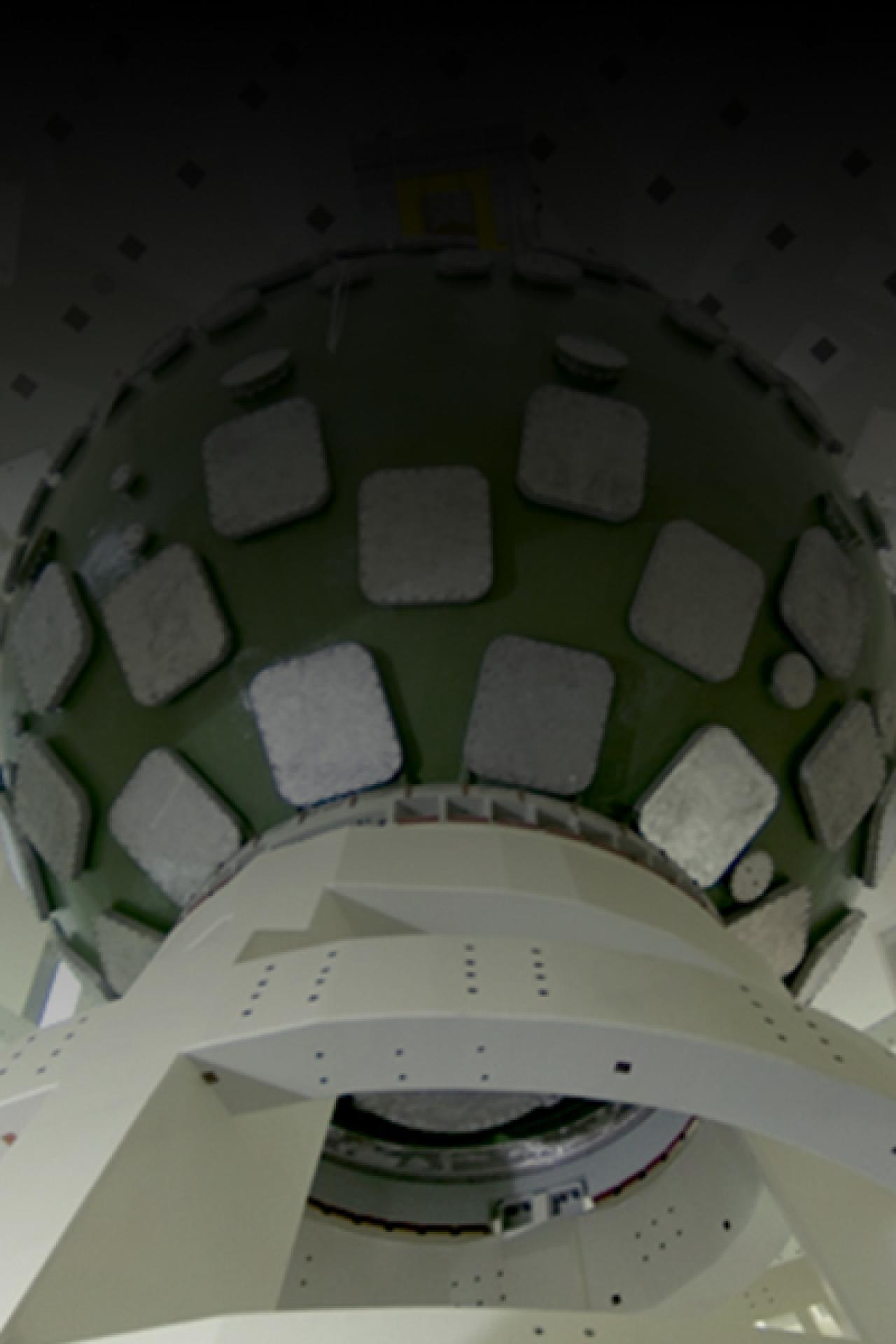
44 systems to align the Megajoule Laser’s beams
Key figures
radian alignment accuracy
units manufactured in medium-scale production
200 sqm ISO 6 clean room

Since 2004, CNIM Systèmes Industriels has been mass-producing high value-added systems for CEA DAM*, namely Frequency Conversion and Laser Beam Focusing Systems (SCF) for the Megajoule Laser (LMJ).
*CEA DAM: French Alternative Energies and Atomic Energy Commission, Military Applications division
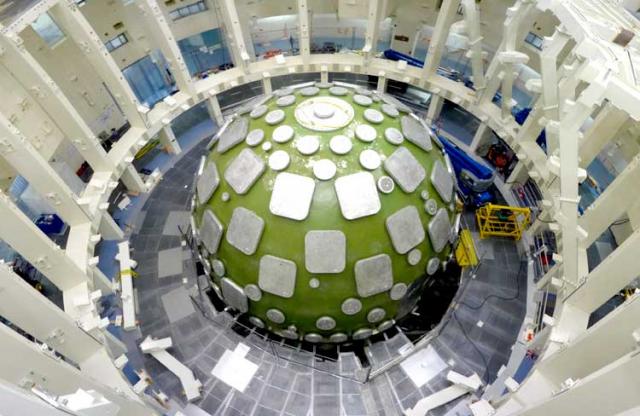
Co-design programme with CEA DAM
The Megajoule Laser (LMJ), commissioned in 2014, is used to study the behaviour of materials under conditions similar to those created by nuclear weapons.
CNIM Systèmes Industriels has been a partner and a major stakeholder in the LMJ programme from its inception in 1996, winning around a dozen contracts.
In 2005, CEA DAM and CNIM Systèmes Industriels began co-designing the 44 Frequency Conversion and Laser Beam Focusing Systems (SCF) installed at the end of each LMJ’s laser beamlines arranged around the experiment room. Their purpose is to convert the frequency of 176 laser beams, focus and aim them at the LMJ target positioned in the centre of the depressurised experiment room.
Following construction of the prototype, and in view of the demonstrated performance, CEA DAM awarded CNIM Systèmes Industriels a private contract in 2010.
Our clean room integration expertise
More info
A large system enabling ultra-precise alignment
Measuring 3 m long, 1.2 m wide and 2.5 m tall, and weighing 1.8 tonnes, SCFs are large, very stable metal structures equipped with optical components.
The alignment accuracy allows to target a target at 8m distance with a precision of 8 μm.

Medium-scale production
The first SCF in the production run was declared operational at the LMJ facility in 2013, contributing to the success of the maiden firing procedure in the experiment room in October 2014. Since then, CNIM Systèmes Industriels has been supplying from 4 to 6 SCFs annually, manufactured in parallel production runs.
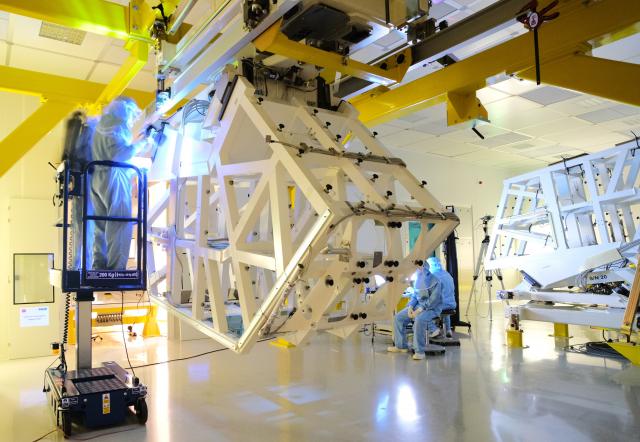
Extremely clean and calibrated to within a micron
After being machined, the component undergoes an ultra-clean washing process in a booth specially designed to accommodate large parts (5 m long, 2.5 m high and 2 m wide). A 20 sq. m room has been specially fitted out to generate ultra-pure water.
Then the SCFs are assembled. This is a critical step in the manufacturing process, requiring a high standard of cleanliness. This operation consists in assembling 1,500 parts in a 220 sqm ISO 6 clean room. System characterisation and calibration are crucial: the LMJ’s lasers must be aimed at a millimetre-scale target with an accuracy of 1 micron.
The final step involves configuring the optical interfaces.
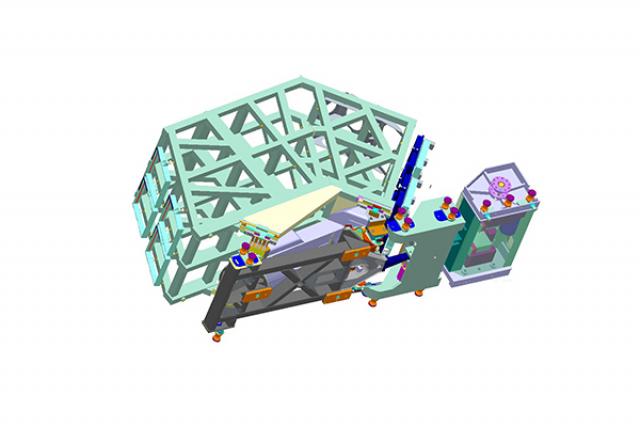
Remotely-operated heavy handling systems
Thanks to its expertise in mechanical engineering, instrumentation and control and computing, and backed by extensive experience with the LMJ programme, CNIM Systèmes Industriels was awarded the contract to design and build the SCF handling systems. These remotely-operated, rail-mounted support systems enable maintenance operations to be performed on the 44 SCFs. They all comply with very stringent cleanliness requirements.
CNIM Systèmes Industriels, also specialist in complex and precision handling systems, supplied the SCF tractor, a wire-guided motorised carriage designed to grasp and manoeuvre an SCF during handling operations. The tractor travels on rails (which it grips with no need for a rack) and is able to climb and descend >50° gradients while carrying a 1.8 tonne load.
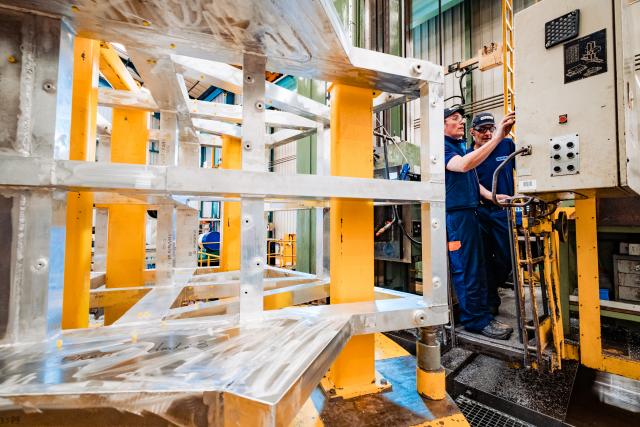
An ideal project for CNIM Systèmes Industriels
This project fits perfectly with CNIM Systèmes Industriels' core strengths, featuring a long-term partnership with the customer, vertical integration and medium-scale production of large components to a very high standard of precision.